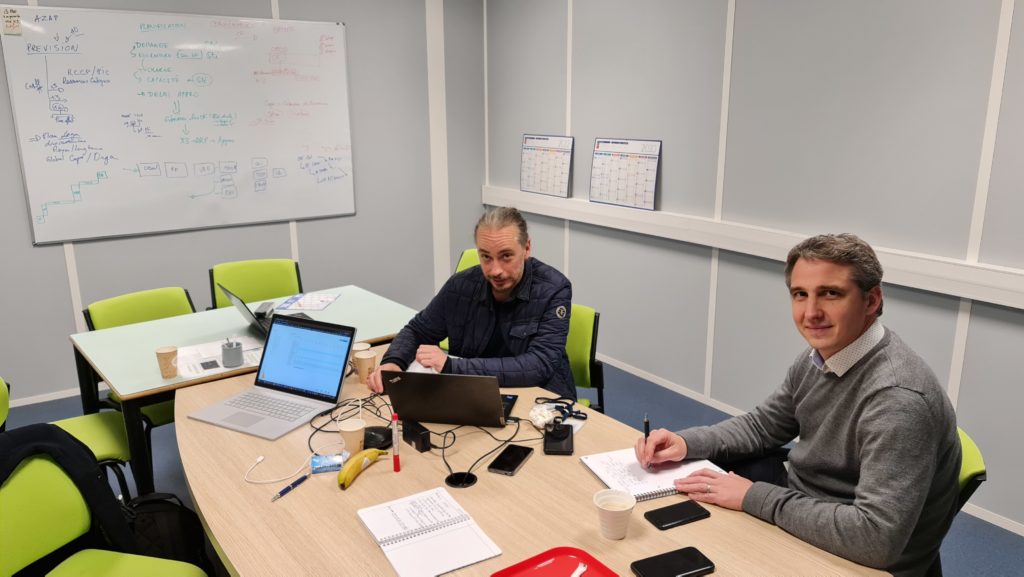
De deux choses l’une,
Soit votre process n’est pas vraiment mûr, et le gain va être de construire ensemble processus et prototype dans Excel pour réaliser la planification. La difficulté sera surtout du côté des planificateurs de pouvoir devenir autonome et efficace dans les extractions de données.
Soit votre process est mûr et vous avez mis au point un Excel alimenté dans lequel vous réalisez votre plan de charge : le gain avec un APS est de disposer tous les matin de votre situation de planification à jour des encours, stocks, commande, prévisions etc…
Dans cette phase de planification, on construit le plan directeur de production. Concrètement on génère et on simule les OF pour remplir les capacités déterminées en PIC.
Quelques mots du métier
On va aussi pouvoir donner des délais aux commandes clients ATP, CTP.
Je sais, ici, il y a toujours un loup chez les consultants. C’est quoi la différence entre ATP et CTP ?
Ecoutez bien, je vais vous dire.
ATP, Available to promise, c’est que pour cette nouvelle commande, vous avez déjà vérifié et engagé les productions qui vont vous générer les stocks dont vous avez besoin pour répondre à cette demande.
CTP, Capable to Promise, c’est que vous vérifiez que tout est dans les délais et les capacités à faire, mais les commandes d’achats ne sont pas passées ni confirmées, et les OF ni planifiés ni lancés.
Planification sous contrainte
Oui, 10 fois oui, mais seulement de la planification sous contrainte manuelle. Mettre en place un APS permet de donner tous les matins une situation de planification à jour : tous les encours, les stocks, les commandes, les prévisions, les nomenclatures et les gammes ont été rafraîchies.
Vous allez pouvoir oublier les heures carrées à extraire ces queries et à les intégrer dans votre Excel.
L’opportunité d’un projet APS est d’abord de disposer du travail d’informaticiens qui vont automatiser ces extractions.
L’APS, lui, va vous permettre d’identifier où les commandes clients seront livrées en retard, où vous avez des excès de charge, de visualiser le cumul des retards de production, de concrétiser des hypothèses de capacité, de simuler l’impact de nouveaux OF sur le appels de composants et de semi-finis et sur les ressources.
Cerise sur le gâteau, vous pourrez aussi leur faire exporter vos nouveaux OF et ne pas avoir à les créer dans l’ERP.
Si vous avez remarqué que je ne vous ai pas parlé de replanification automatisée sous contrainte, ce n’est pas un oubli, c’est un débat philosophique. Après si c’est un défi, challenge accepted, mais attention, on bascule dans la rocket science.